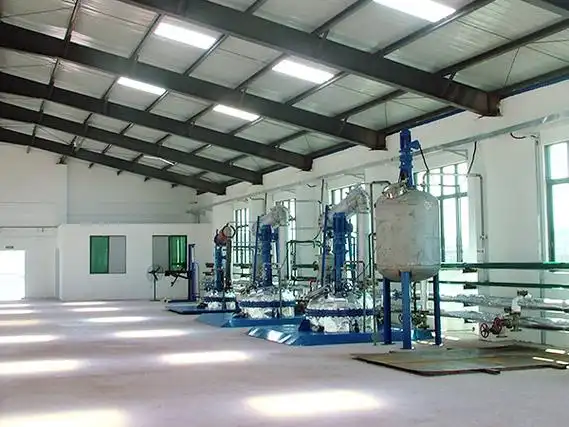
**涂料的干燥时间与固化过程:影响因素及优化方法**
涂料的干燥与固化是涂层形成的关键阶段,直接影响涂膜的性能和外观。干燥通常指溶剂挥发形成物理固态膜的过程,而固化则涉及树脂的交联反应,形成化学稳定的三维网络结构。两者共同决定涂层的硬度、附着力及耐候性。
**影响因素:**
1. **环境条件**:温度与湿度是因素。温度升高加速溶剂挥发和反应速率,但过高可能导致表面结皮而内部残留溶剂;湿度过高会延缓水性涂料干燥,并可能引起冷凝或发白现象。
2. **涂料配方**:溶剂类型(如快干溶剂或慢干溶剂)、树脂种类(如环氧树脂需固化剂)、固含量及添加剂(如催化剂)均显著影响干燥固化效率。
3. **施工工艺**:涂层过厚易导致表干内湿,引发起泡或开裂;喷涂均匀性不足可能造成局部固化不良。
4. **基材特性**:多孔基材会吸收溶剂,缩短干燥时间但可能削弱附着力;金属基材导热快,可能加速固化。
**优化方法:**
1. **配方调整**:采用高固含或UV固化树脂减少溶剂依赖;添加催干剂或交联剂以缩短固化时间。
2. **工艺控制**:通过多层薄涂替代单层厚涂,确保溶剂充分挥发;优化烘烤温度曲线,避免热应力导致缺陷。
3. **环境调控**:使用除湿机或加热设备维持温湿度稳定(如25℃、50%RH);加强通风以加速溶剂扩散。
4. **技术升级**:引入红外或紫外固化设备,实现局部快速固化;对特殊基材进行预热或底漆处理,改善涂层均匀性。
**总结**:通过科学配比、工艺及环境管理,可有效平衡干燥速度与涂膜性能,避免橘皮、等缺陷,提升涂装效率与质量。不同应用场景(如汽车、家具)需针对性优化,以实现与耐久性的统一。